Tability is a cheatcode for goal-driven teams. Set perfect OKRs with AI, stay focused on the work that matters.
What are Quality Control Manager OKRs?
The Objective and Key Results (OKR) framework is a simple goal-setting methodology that was introduced at Intel by Andy Grove in the 70s. It became popular after John Doerr introduced it to Google in the 90s, and it's now used by teams of all sizes to set and track ambitious goals at scale.
How you write your OKRs can make a huge difference on the impact that your team will have at the end of the quarter. But, it's not always easy to write a quarterly plan that focuses on outcomes instead of projects.
We have curated a selection of OKR examples specifically for Quality Control Manager to assist you. Feel free to explore the templates below for inspiration in setting your own goals.
If you want to learn more about the framework, you can read our OKR guide online.
The best tools for writing perfect Quality Control Manager OKRs
Here are 2 tools that can help you draft your OKRs in no time.
Tability AI: to generate OKRs based on a prompt
Tability AI allows you to describe your goals in a prompt, and generate a fully editable OKR template in seconds.
- 1. Create a Tability account
- 2. Click on the Generate goals using AI
- 3. Describe your goals in a prompt
- 4. Get your fully editable OKR template
- 5. Publish to start tracking progress and get automated OKR dashboards
Watch the video below to see it in action 👇
Tability Feedback: to improve existing OKRs
You can use Tability's AI feedback to improve your OKRs if you already have existing goals.
- 1. Create your Tability account
- 2. Add your existing OKRs (you can import them from a spreadsheet)
- 3. Click on Generate analysis
- 4. Review the suggestions and decide to accept or dismiss them
- 5. Publish to start tracking progress and get automated OKR dashboards
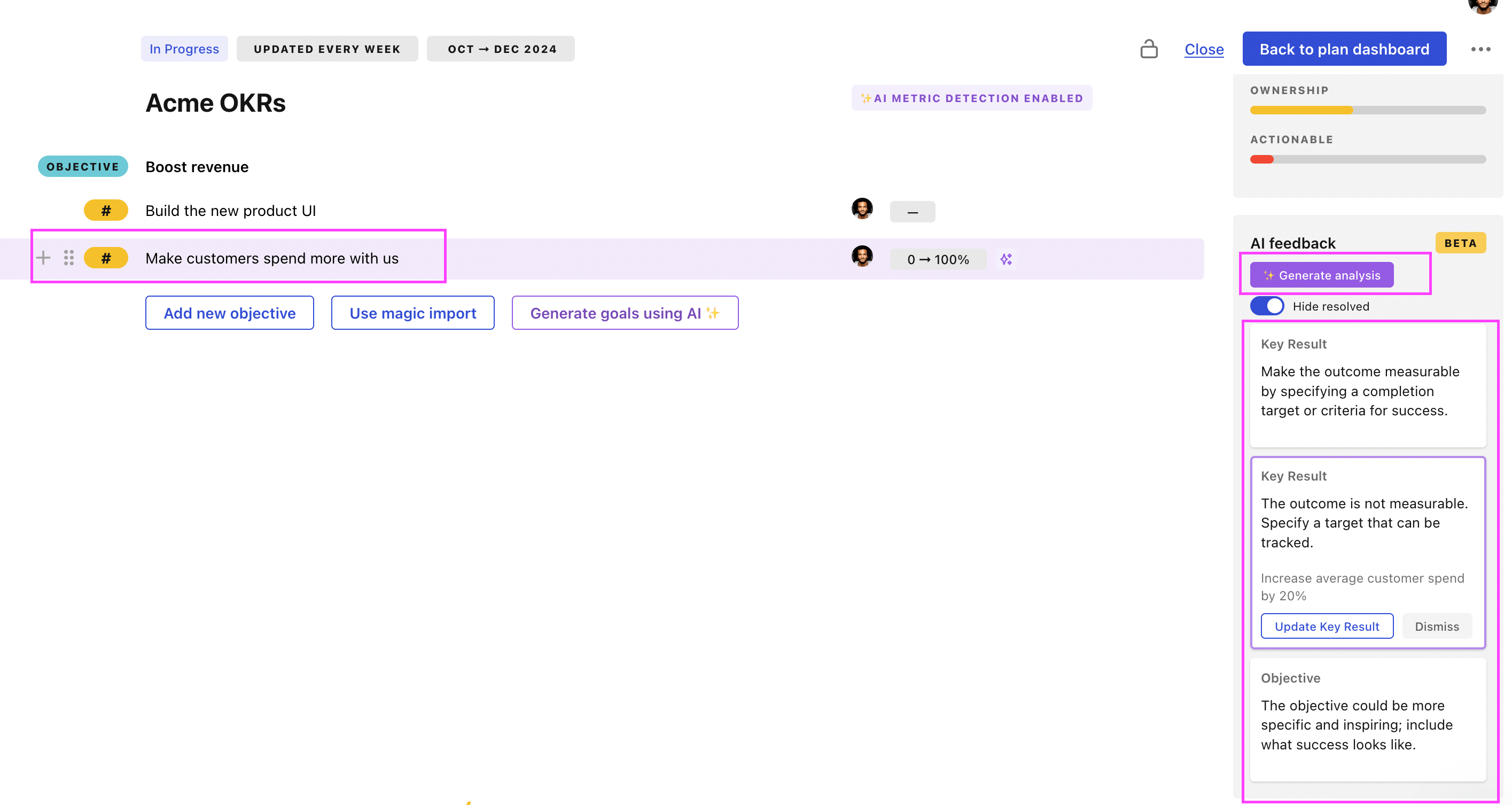
Tability will scan your OKRs and offer different suggestions to improve them. This can range from a small rewrite of a statement to make it clearer to a complete rewrite of the entire OKR.
Quality Control Manager OKRs examples
We've added many examples of Quality Control Manager Objectives and Key Results, but we did not stop there. Understanding the difference between OKRs and projects is important, so we also added examples of strategic initiatives that relate to the OKRs.
Hope you'll find this helpful!
OKRs to streamline quality control process
ObjectiveStreamline quality control process
KRImplement a digital QC tracking system by 30% project completion
Train staff on new software usage
Research and select suitable digital QC tracking software
Develop an implementation plan, set up and test the system
KRImprove speed of QC process by 15%
Provide training to enhance team proficiency
Streamline QC procedures for efficiency
Implement automation in repetitive QC steps
KRDecrease QC-related errors by 20%
Implement regular training programs to boost QC team skill levels
Introduce advanced QA/QC software for error reduction
Regularly update QC protocols and checklists
OKRs to enhance product quality and shipment speed
ObjectiveEnhance product quality and shipment speed
KRIncrease shipping speed by 15% through operational efficiencies
Assess and eliminate bottlenecks in the delivery process
Implement automated packaging systems to minimize processing time
Prioritize streamlined routing in distribution centers
KRImplement quality control system to decrease customer returns by 10%
Develop and implement selected quality control system
Research and identify effective quality control systems
Track, analyze, and adjust system based on results
KRReduce product defect rates by 20% through improvement initiatives
Invest in superior raw materials for product creation
Train production staff on improved manufacturing techniques
Implement rigorous quality control checks in the production process
OKRs to enhance architectural vision and delivery quality
ObjectiveEnhance architectural vision and delivery quality
KRAchieve 90% client satisfaction rating for completed architectural projects
Foster open communication for client queries
Regularly monitor and evaluate client satisfaction
Implement client feedback in final project designs
KRIncrease departmental collaboration on innovative design concepts
Create shared online platform for design ideas discussion
Establish interdisciplinary project teams for innovation design
Implement regular brainstorming sessions across different departments
KRImplement 2 new quality control measures to optimize project delivery
Research effective quality control methods to address deficiencies
Identify two deficiencies in the current project delivery process
Develop and implement quality control measures based on research
OKRs to increase the customer return rate
ObjectiveIncrease the customer return rate
KRGrow repeat customer base by 15% through personalized promotional deals
Identify top-selling products for personalized deal targeting
Implement a customer loyalty program with exclusive deals
Analyze customer buying habits to offer tailored promotions
KRBoost customer satisfaction score by 20% to encourage repeat purchases
Improve product quality based on customer feedback
Offer regular deals or loyalty incentives
Implement customer service training for staff members
KRReduce the product return rate by 10% by improving product quality control
Train staff regularly on quality control procedures and standards
Implement thorough testing protocols for all product manufacturing stages
Regularly review and update quality control measures
OKRs to enhance efficiency in printing production lineup
ObjectiveEnhance efficiency in printing production lineup
KRReduce printing error rate by 10% through quality control procedures
Regularly update printer software and drivers
Train staff on correct printing procedures
Implement regular checks and maintenance of printers
KRDecrease production turnaround time by 7% via improved supply chain management
Implement real-time tracking for supply chain efficiency
Provide staff training for efficient inventory management
Streamline procurement processes to reduce lead times
KRIncrease throughput by 15% using optimized workflow management
Identify current bottlenecks in the operation workflow
Implement an automated workflow management system
Train staff on optimized workflow best practices
OKRs to maximize Efficiency of Supplier Performance
ObjectiveMaximize Efficiency of Supplier Performance
KRReduce supplier-related issues/complaints by 30%
Improve communication channels with suppliers for better understanding
Implement regular quality control checks
Offer continuous feedback to suppliers
KRIncrease supplier on-time delivery rate by 20%
Regularly evaluate and feedback suppliers on performance
Establish strict delivery deadlines for all vendors
Implement a real-time supplier delivery tracking system
KRImprove Supplier Quality Score by 15%
Enhance supplier training and certification processes
Regularly evaluate and review supplier performance
Implement stricter quality control checks on received supplies
OKRs to enhance quality in document management processes
ObjectiveEnhance quality in document management processes
KRReduce document-related errors by 30% through implementing quality controls
Implement thorough document review procedures for error identification
Introduce an effective quality control system in the workflow
Conduct regular training sessions for staff on document accuracy
KRTrain 90% of staff in new document management practices to ensure standardization
Monitor and confirm staff training completion
Identify relevant staff for document management training
Arrange training sessions on new practices
KRStreamline 25% of existing document flows for improved efficiency by end of quarter
Develop and implement strategies to improve identified processes
Monitor and evaluate efficiency improvements
Identify and analyze current document flows for inefficiencies
OKRs to ensure all product lines attain organic certification
ObjectiveEnsure all product lines attain organic certification
KRAchieve 100% compliance with organic certification standards
Research current guidelines for organic certification standards
Implement needed changes to meet those standards
Initiate the certification process
KRObtain organic source materials for 100% of our products
Initiate partnerships with chosen organic suppliers
Identify potential suppliers of organic raw materials
Monitor quality control of sourced organic materials
KRSubmit all products for organic certification evaluation
Submit applications to the relevant certification body
Fill and complete relevant certification application forms
Gather all product details required for organic certification
OKRs to enhance customer experience satisfaction
ObjectiveEnhance customer experience satisfaction
KRIncrease overall customer satisfaction rating by 10%
Promptly address and resolve customer complaints
Implement customer feedback surveys after purchases
Organize regular staff customer service training
KRAchieve 20% repeat business from existing customers
Implement personalized email marketing campaigns targeting existing customers
Develop a loyalty program for incentivizing repeat purchases
Provide excellent customer service to encourage return visits
KRReduce customer complaint frequency by 15%
Implement comprehensive staff training for customer service improvement
Enhance customer feedback collection mechanisms
Develop efficient quality control measures
OKRs to enhance production quality to reduce issue occurrence
ObjectiveEnhance production quality to reduce issue occurrence
KRIncrease testing coverage by 25% to identify pending issues
Identify areas with lacking testing coverage immediately
Prioritize testing the system functionalities more rigorously
Allocate additional resources to expand testing protocols
KRConduct two production quality control trainings for staff
Develop detailed, engaging training materials for both sessions
Identify relevant topics for two production quality control trainings
Schedule and carry out the two training sessions
KRReduce production defect rate by 15% through process optimization
Monitor, evaluate the new process's performance regularly
Implement targeted changes to optimize efficiency and quality
Analyze existing production process for potential areas of improvement
Quality Control Manager OKR best practices
Generally speaking, your objectives should be ambitious yet achievable, and your key results should be measurable and time-bound (using the SMART framework can be helpful). It is also recommended to list strategic initiatives under your key results, as it'll help you avoid the common mistake of listing projects in your KRs.
Here are a couple of best practices extracted from our OKR implementation guide 👇
Tip #1: Limit the number of key results
Having too many OKRs is the #1 mistake that teams make when adopting the framework. The problem with tracking too many competing goals is that it will be hard for your team to know what really matters.
We recommend having 3-4 objectives, and 3-4 key results per objective. A platform like Tability can run audits on your data to help you identify the plans that have too many goals.
Tip #2: Commit to weekly OKR check-ins
Setting good goals can be challenging, but without regular check-ins, your team will struggle to make progress. We recommend that you track your OKRs weekly to get the full benefits from the framework.
Being able to see trends for your key results will also keep yourself honest.
Tip #3: No more than 2 yellow statuses in a row
Yes, this is another tip for goal-tracking instead of goal-setting (but you'll get plenty of OKR examples above). But, once you have your goals defined, it will be your ability to keep the right sense of urgency that will make the difference.
As a rule of thumb, it's best to avoid having more than 2 yellow/at risk statuses in a row.
Make a call on the 3rd update. You should be either back on track, or off track. This sounds harsh but it's the best way to signal risks early enough to fix things.
Save hours with automated Quality Control Manager OKR dashboards
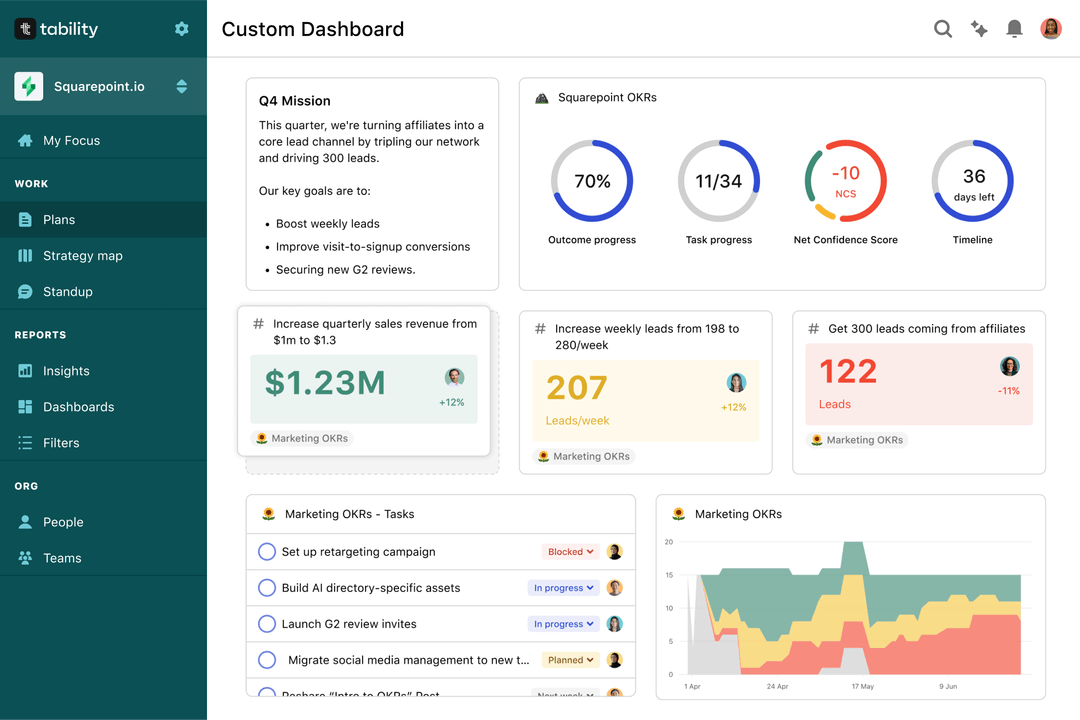
The rules of OKRs are simple. Quarterly OKRs should be tracked weekly, and yearly OKRs should be tracked monthly. Reviewing progress periodically has several advantages:
- It brings the goals back to the top of the mind
- It will highlight poorly set OKRs
- It will surface execution risks
- It improves transparency and accountability
Spreadsheets are enough to get started. Then, once you need to scale you can use Tability to save time with automated OKR dashboards, data connectors, and actionable insights.
How to get Tability dashboards:
- 1. Create a Tability account
- 2. Use the importers to add your OKRs (works with any spreadsheet or doc)
- 3. Publish your OKR plan
That's it! Tability will instantly get access to 10+ dashboards to monitor progress, visualise trends, and identify risks early.
More Quality Control Manager OKR templates
We have more templates to help you draft your team goals and OKRs.
OKRs to boost the success rate in timely financial statement reporting
OKRs to optimize the tutoring process for improved efficiency and effectiveness
OKRs to ensure sustainability of the financial business
OKRs to achieve a passing grade in English class
OKRs to develop a Security Officer Performance Appraisal Plan for an Irish client
OKRs to improve leadership skills